¿Cómo se mecanizan las piezas de alta precisión?
2023-09-22
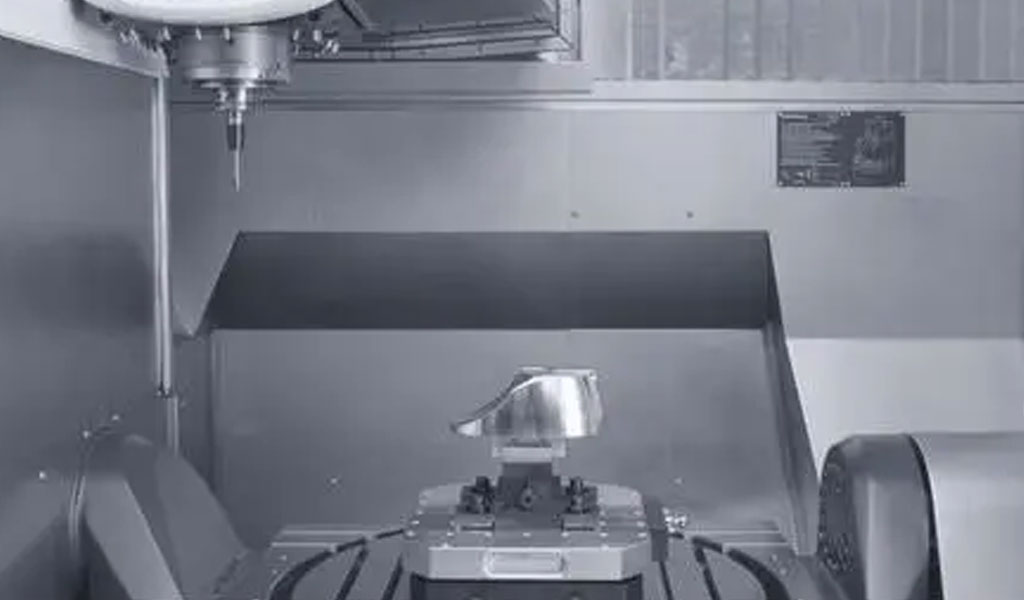
Comprender el mecanizado de precisión
El mecanizado de precisión es una piedra angular de la fabricación moderna, responsable de producir componentes complejos y precisos utilizados en una amplia gama de industrias. Para comprender plenamente su importancia, exploremos los conceptos centrales del mecanizado de precisión, su papel vital en diversos sectores y el recorrido histórico que lo ha llevado a su estado actual de excelencia.A. ¿Qué es el mecanizado de precisión?
El mecanizado de precisión se refiere a un conjunto de procesos de fabricación que eliminan material de una pieza de trabajo con un alto grado de precisión y control, lo que da como resultado componentes finamente elaborados con tolerancias estrictas. Este proceso transforma materias primas, como metales, plásticos o cerámicas, en piezas precisas que cumplen especificaciones exactas. Las características clave del mecanizado de precisión incluyen:- Exactitud: El mecanizado de precisión garantiza que el producto final se ajuste exactamente al diseño previsto, con una desviación mínima.
- Tolerancias ajustadas: Permite la producción de piezas con tolerancias extremadamente estrictas, lo que significa que los componentes terminados se ajustan estrictamente a las medidas especificadas.
- Acabado superficial superior: El mecanizado de precisión proporciona acabados superficiales excepcionales, eliminando a menudo la necesidad de procesos de acabado adicionales.
- Geometrías complejas: Puede crear formas, contornos y características intrincadas, lo que lo hace indispensable en la fabricación de componentes con diseños complejos.
- repetibilidad: Precisión proceso de mecanizadoson altamente repetibles, lo que garantiza una calidad constante en múltiples piezas.
- Versatilidad: Puede aplicarse a una amplia gama de materiales, lo que lo hace adecuado para diversas industrias.
B. Importancia del mecanizado de precisión
El mecanizado de precisión tiene una inmensa importancia en varias industrias críticas y afecta varios aspectos de nuestra vida diaria. Aquí hay algunas razones de peso de su importancia:- Industria aeroespacial: En el sector aeroespacial, el mecanizado de precisión es indispensable para fabricar componentes que resistan condiciones extremas. Motores de avión, aterrizaje. equipoy los elementos estructurales dependen de piezas mecanizadas con precisión para su seguridad y rendimiento.
- Dispositivos médicos: Los dispositivos médicos como instrumentos quirúrgicos, prótesis y dispositivos implantables requieren un mecanizado de precisión para lograr biocompatibilidad, exactitud y seguridad del paciente.
- Sector automotriz: Las piezas mecanizadas con precisión son esenciales para que la industria automotriz garantice la confiabilidad y eficiencia de los vehículos. Componentes como piezas de motor, sistemas de transmisión y mecanismos de freno dependen de un mecanizado preciso.
- Electrónica y semiconductores: El mecanizado de precisión es fundamental en la producción de componentes microelectrónicos y dispositivos semiconductores, donde las tolerancias minúsculas son imperativas para la funcionalidad.
- Sector energético: La industria energética depende del mecanizado de precisión para la producción de piezas críticas utilizadas en la generación de energía, incluidas turbinas, generadores y componentes de transmisión.
- Fabricación de herramientas y matrices: El mecanizado de precisión es crucial en la fabricación de herramientas y matrices, que, a su vez, se utilizan para crear muchos otros productos.
- Electrónica de consumo : La producción de teléfonos inteligentes, computadoras portátiles y otros productos electrónicos de consumo se beneficia del mecanizado de precisión para garantizar diseños elegantes y una funcionalidad óptima.
- Investigación y desarrollo: Los investigadores y científicos dependen de componentes mecanizados con precisión para experimentos, prototipos y equipos de laboratorio.
C. Perspectiva histórica
El viaje del mecanizado de precisión se remonta a civilizaciones antiguas, donde hábiles artesanos utilizaban herramientas rudimentarias para dar forma a los materiales. Sin embargo, la precisión lograda en aquellos tiempos era limitada en comparación con los estándares contemporáneos.- Mecanizado de precisión inicial: La revolución industrial de los siglos XVIII y XIX marcó un período crucial en el desarrollo del mecanizado de precisión. La invención de las máquinas herramienta, como los tornos y las fresadoras, revolucionó la fabricación al permitir una mayor precisión y coherencia.
- Segunda Guerra Mundial: El mecanizado de precisión jugó un papel fundamental en la Segunda Guerra Mundial, ya que era esencial para producir equipos militares con la precisión y uniformidad requeridas. Esta era fue testigo de avances en las técnicas de mecanizado y la aparición de nuevos materiales.
- Avances de posguerra: El período de posguerra vio un aumento en las innovaciones tecnológicas, incluido el uso de máquinas de control numérico por computadora (CNC). Mecanizado CNC permitió operaciones automatizadas y de alta precisión, marcando el comienzo de una nueva era de fabricación.
- La era digital: La integración de computadoras y software en los procesos de mecanizado ha elevado aún más el mecanizado de precisión. Las máquinas CNC modernas pueden ejecutar operaciones complejas con una precisión incomparable, lo que las hace indispensables en el panorama de fabricación actual.
Materiales y su significado
Los materiales son la base del mecanizado de precisión y la selección del material adecuado juega un papel fundamental en la producción de piezas de alta precisión. En esta sección, profundizaremos en la importancia de seleccionar los materiales adecuados, comprenderemos la importancia de las propiedades de los materiales y exploraremos los diversos factores que afectan la maquinabilidad.A. Selección de materiales
La elección de materiales en el mecanizado de precisión es una decisión crítica que impacta directamente en el rendimiento, la durabilidad y la funcionalidad del producto final. Los fabricantes deben considerar varios factores al seleccionar materiales:- Idoneidad de los materiales: El material debe ser adecuado para la aplicación prevista. Las diferentes industrias y aplicaciones tienen distintos requisitos, como resistencia a la temperatura, resistencia a la corrosión y conductividad eléctrica.
- Propiedades mecánicas: Las propiedades mecánicas como la resistencia a la tracción, la dureza y la ductilidad son cruciales. Por ejemplo, en el sector aeroespacial, se prefieren materiales con alta resistencia a la tracción para los componentes estructurales.
- Propiedades termales: Algunas aplicaciones requieren materiales con excelente conductividad térmica o resistencia a altas temperaturas. Esto es especialmente importante en industrias como la generación de energía y la electrónica.
- Resistencia a la Corrosión: En entornos donde la corrosión es un problema, se prefieren materiales con alta resistencia a la corrosión, como acero inoxidable o titanio.
- Consideraciones de peso: Industrias como la automovilística y la aeroespacial a menudo dan prioridad a materiales ligeros como el aluminio o los compuestos de fibra de carbono para reducir el consumo de combustible y mejorar el rendimiento.
- Restricciones de costo: El costo es un factor importante en la selección de materiales. Los materiales de alto rendimiento pueden ser costosos, por lo que los fabricantes deben lograr un equilibrio entre rendimiento y rentabilidad.
- Cumplimiento Regulatorio: En industrias como la atención médica, los materiales deben cumplir estrictos estándares regulatorios de biocompatibilidad y seguridad.
- Disponibilidad: La disponibilidad de materiales y sus fuentes también afectan la selección. Algunas aleaciones o compuestos especializados pueden tener disponibilidad limitada.
B. Propiedades de los materiales
Comprender las propiedades de los materiales es crucial para el mecanizado de precisión. A continuación se muestran algunas propiedades clave de los materiales y su importancia:- Resistencia a la tracción: La resistencia a la tracción mide la capacidad de un material para resistir una fuerza de tracción sin romperse. Es esencial para componentes estructurales y piezas sometidas a esfuerzos mecánicos.
- Dureza: La dureza indica la resistencia de un material a la deformación y al desgaste. Los materiales duros son adecuados para herramientas de corte, mientras que pueden preferirse materiales más blandos para determinadas aplicaciones, como juntas.
- Ductilidad: La ductilidad se refiere a la capacidad de un material para deformarse sin romperse cuando se somete a un esfuerzo de tracción. Los materiales dúctiles son más fáciles de moldear pero pueden no ser adecuados para aplicaciones que requieren rigidez.
- Conductividad Térmica: Los materiales con alta conductividad térmica disipan el calor de manera eficiente. Esta propiedad es vital en aplicaciones donde el control de la temperatura es crítico.
- Conductividad eléctrica: La conductividad eléctrica es esencial en la electrónica y los componentes eléctricos, donde los materiales deben facilitar el flujo de electricidad.
- Propiedades magnéticas: Las propiedades magnéticas son importantes en industrias como la electromagnética y la electrónica, donde es posible que los materiales deban ser ferromagnéticos o no magnéticos.
- Resistencia química: Los materiales deben resistir la corrosión química en ambientes donde están expuestos a ácidos, bases u otras sustancias corrosivas.
C. Factores de maquinabilidad
La maquinabilidad se refiere a la facilidad con la que un material puede ser mecanizado, cortado o moldeado. Está influenciado por varios factores, entre ellos:- Dureza material: Los materiales más blandos generalmente son más fáciles de mecanizar, mientras que los materiales más duros pueden requerir herramientas y técnicas especializadas.
- Formación de virutas: La formación y evacuación de virutas durante el mecanizado afectan la eficiencia del proceso y el acabado superficial.
- Desgaste de la herramienta: Diferentes materiales pueden causar distintos grados de desgaste de la herramienta, lo que afecta la velocidad y el costo del mecanizado.
- Refrigerante y Lubricación: El refrigerante y la lubricación adecuados son esenciales para reducir la fricción, el calor y el desgaste de las herramientas durante el mecanizado.
- Velocidad cortante: La velocidad a la que la herramienta de corte se mueve a través del material afecta tanto a la productividad como a la calidad de la superficie mecanizada.
- Material de la herramienta: La elección del material de la herramienta de corte, como carburo o acero de alta velocidad, depende del material que se mecaniza.
- Parámetros de corte: Ajustar los parámetros de corte como la velocidad de avance y la profundidad de corte puede optimizar el proceso de mecanizado para materiales específicos.
Máquinas herramienta para mecanizado de precisión
Las máquinas herramienta son el corazón del mecanizado de precisión y permiten la transformación de materias primas en piezas de alta precisión. En esta sección, exploraremos cuatro tipos clave de máquinas herramienta utilizadas en el mecanizado de precisión: centros de mecanizado CNC, tornos, rectificadoras y electroerosión (mecanizado por descarga eléctrica). Cada una de estas máquinas desempeña un papel único en la producción de componentes precisos.A. Centros de mecanizado CNC
Los centros de mecanizado CNC (Control Numérico por Computadora) son versátiles y ampliamente utilizados en el mecanizado de precisión. Son sistemas automatizados que controlan el movimiento de herramientas de corte y piezas de trabajo con una precisión excepcional. A continuación se ofrece una descripción general de los centros de mecanizado CNC y su importancia:- Versatilidad: Los centros de mecanizado CNC pueden realizar diversas operaciones de mecanizado, incluidos fresado, taladrado y roscado. Esta versatilidad permite la producción de piezas complejas con múltiples características.
- Alta precisión: El control computarizado de las máquinas CNC garantiza un posicionamiento preciso de las herramientas y resultados consistentes, lo que las hace ideales para piezas con tolerancias estrictas.
- Automatización : Los centros de mecanizado CNC pueden funcionar de forma continua, con una mínima intervención humana. Esta automatización aumenta la eficiencia y reduce el riesgo de errores.
- Geometrías complejas: Destacan en el mecanizado de formas y contornos complejos, lo que los hace adecuados para industrias como la aeroespacial, donde los componentes complejos son comunes.
- Resultados repetibles: Las máquinas CNC ofrecen una excelente repetibilidad, lo que garantiza que cada pieza producida coincida con las especificaciones exactas del diseño.
- Tiempos de configuración reducidos: Los centros de mecanizado CNC se pueden programar para cambiar rápidamente entre diferentes tareas, minimizando los tiempos de configuración y aumentando la eficiencia de la producción.
B. Máquinas de torneado
Los tornos se utilizan para crear piezas cilíndricas girando una pieza de trabajo mientras una herramienta de corte elimina material de su superficie exterior. Son esenciales para producir ejes, pasadores y otros componentes con simetría rotacional. Los puntos clave sobre los tornos incluyen:- Piezas cilíndricas: Los tornos se especializan en producir componentes cilíndricos o tubulares, incluidos aquellos con roscas o ranuras intrincadas.
- Altas velocidades: Funcionan a altas velocidades, lo que los hace adecuados para piezas que requieren un acabado suave y preciso.
- Operación de un solo eje: La mayoría de los tornos son de un solo eje y se centran en dar forma a la superficie externa de la pieza de trabajo.
- Eficiente para la producción en masa: El torneado es muy eficiente para la producción de piezas en masa con un mínimo desperdicio de material.
- Máquinas de torno: Las máquinas de torno manuales y controladas por CNC son máquinas de torneado de uso común y ofrecen una variedad de capacidades.
C. Rectificadoras
Las máquinas rectificadoras están diseñadas para el acabado superficial de precisión y el modelado de materiales duros o abrasivos. Son cruciales para lograr tolerancias extremadamente estrictas y acabados superficiales superiores. He aquí por qué las rectificadoras son importantes:- Precisión a nivel de micras: Las máquinas rectificadoras pueden alcanzar una precisión a nivel de micras, lo que las hace esenciales para aplicaciones que exigen el más alto nivel de precisión.
- Eliminación de material: Eliminan material por abrasión, permitiendo corregir imperfecciones superficiales y consiguiendo una suavidad excepcional.
- Rectificado de herramientas y cortadores: Además del rectificado de superficies, existen rectificadoras especializadas para afilar herramientas de corte y producir perfiles precisos.
- Variedad de métodos de molienda: Los diferentes tipos de rectificadoras, incluidas las rectificadoras de superficie, las rectificadoras cilíndricas y las rectificadoras sin centros, satisfacen diversas necesidades de mecanizado.
- Materiales endurecidos: El rectificado es especialmente adecuado para materiales endurecidos como acero para herramientas y cerámica, donde los métodos de mecanizado tradicionales pueden resultar ineficaces.
D. EDM (mecanizado por descarga eléctrica)
EDM, o mecanizado por descarga eléctrica, es un proceso de mecanizado no tradicional que utiliza descargas eléctricas para dar forma a los materiales. Es ideal para crear piezas intrincadas y delicadas donde las herramientas de corte tradicionales pueden causar daños. Los aspectos clave de la electroerosión incluyen:- Sin contacto físico: La electroerosión no implica contacto físico directo entre la herramienta y la pieza de trabajo, lo que minimiza el riesgo de desgaste de la herramienta y daños a materiales frágiles.
- Alta precisión: Puede lograr alta precisión y calidad de acabado superficial, incluso con materiales excepcionalmente duros.
- Electroerosión por hilo y electroerosión por plomo: Hay dos tipos principales de máquinas de electroerosión: corte de alambre La electroerosión, que utiliza un electrodo de alambre, y la electroerosión por plomo, que utiliza un electrodo moldeado.
- Formas complejas: La electroerosión puede producir formas complejas, como matrices y moldes, con detalles intrincados y características finas.
- Zona afectada por el calor: Dado que la electroerosión no genera calor en la pieza de trabajo, es adecuada para materiales sensibles al calor como las aleaciones aeroespaciales.
- Proceso lento: La electroerosión es relativamente lenta en comparación con otros métodos de mecanizado, lo que la hace más adecuada para trabajos de baja cantidad y alta precisión.
Herramientas de corte y utillaje
Las herramientas de corte están a la vanguardia del mecanizado de precisión y sirven como instrumentos que dan forma y transforman las materias primas en piezas de alta precisión. En esta sección, exploraremos los distintos tipos de herramientas de corte, la importancia de los recubrimientos de las herramientas y los factores que afectan la vida útil y el desgaste de las herramientas.A. Tipos de herramientas de corte
El mecanizado de precisión se basa en una amplia gama de herramientas de corte, cada una diseñada para tareas y materiales específicos. La elección de la herramienta de corte influye en gran medida en la eficiencia y precisión del proceso de mecanizado. A continuación se muestran algunos tipos comunes de herramientas de corte:- Molinos de extremo: Las fresas finales son herramientas versátiles que se utilizan para operaciones de fresado. Tienen múltiples filos de corte y pueden eliminar material de la pieza de trabajo de varias maneras, incluido el refrentado, el contorneado y el ranurado.
- Taladros: Las brocas están diseñadas para crear agujeros en piezas de trabajo. Vienen en varias formas, incluidas brocas helicoidales, brocas centrales y brocas indexables.
- Insertos de torneado: Se utilizan en tornos para dar forma a piezas cilíndricas. Las plaquitas de torneado están disponibles en una variedad de formas y materiales para adaptarse a diferentes aplicaciones.
- Fresas: Las fresas vienen en diferentes formas, como fresas de planear, molinos de bolas y fresas para ranurar, y se utilizan en fresadoras para crear diversas características en la pieza de trabajo.
- Reamers: Los escariadores se utilizan para terminar y dimensionar orificios previamente perforados hasta obtener dimensiones precisas. Garantizan superficies de orificios suaves y precisas.
- Grifos y matrices: Estas herramientas de corte se utilizan para operaciones de roscado. Los machos crean roscas internas, mientras que los troqueles crean roscas externas.
- Muelas abrasivas: Las muelas abrasivas son herramientas abrasivas que se utilizan para el rectificado de superficies de precisión. Están disponibles en varios materiales abrasivos y tamaños de grano.
- Brochas: Las brochas son herramientas especializadas que se utilizan para cortar formas y perfiles internos y externos, como chaveteros y ranuras.
- Avellanados y avellanadores: Estas herramientas se utilizan para crear huecos o chaflanes alrededor de agujeros para cierres.
- Barras aburridas: Las barras de mandrinar se utilizan en operaciones de mandrinado para ampliar los agujeros existentes con precisión.
B. Recubrimientos de herramientas
Los recubrimientos para herramientas son capas delgadas de material que se aplican a las herramientas de corte para mejorar su rendimiento y durabilidad. Estos recubrimientos ofrecen varias ventajas:- Fricción reducida: Los recubrimientos como el nitruro de titanio (TiN) y el carbonitruro de titanio (TiCN) reducen la fricción entre la herramienta y la pieza de trabajo, lo que produce un corte más suave y una vida útil más larga de la herramienta.
- Dureza mejorada: Los recubrimientos aumentan la dureza de la superficie de la herramienta, haciéndola más resistente al desgaste y extendiendo la vida útil de la herramienta.
- Resistencia al calor mejorada: Los recubrimientos pueden soportar las altas temperaturas generadas durante el mecanizado, lo que reduce el desgaste de las herramientas relacionado con el calor y aumenta las velocidades de corte.
- Propiedades anti-acumulación: Algunos recubrimientos tienen propiedades antiadherentes, lo que evita la acumulación de material en los bordes cortantes de la herramienta.
- Mayor lubricidad: Las herramientas recubiertas tienen una lubricidad mejorada, lo que reduce la necesidad de un exceso de refrigerante y mejora la evacuación de virutas.
C. Vida útil y desgaste de la herramienta
Comprender la vida útil y el desgaste de las herramientas es crucial para optimizar los procesos de mecanizado y minimizar los costos de producción. La vida útil de la herramienta se refiere al tiempo que una herramienta de corte permanece efectiva antes de que sea necesario reemplazarla o reacondicionarla. Varios factores influyen en la vida útil y el desgaste de la herramienta:- Velocidad cortante: Las velocidades de corte más altas pueden provocar un mayor desgaste de la herramienta debido a las temperaturas más altas generadas durante el mecanizado. La selección adecuada de velocidades de corte es esencial para equilibrar la vida útil de la herramienta y la productividad.
- Tasa de alimentación: La velocidad a la que la herramienta de corte avanza hacia la pieza de trabajo afecta el desgaste de la herramienta. Los avances altos pueden acelerar el desgaste, mientras que los avances más bajos pueden prolongar la vida útil de la herramienta.
- Profundidad del corte: La profundidad del corte influye en la cantidad de material eliminado por pasada. Los cortes más profundos pueden aumentar el desgaste de la herramienta, por lo que optimizar la profundidad es fundamental.
- Dureza material: Cortar materiales duros puede acelerar el desgaste de la herramienta. Se utilizan herramientas y revestimientos especializados para mecanizar materiales duros de forma eficaz.
- Refrigerante y Lubricación: El refrigerante y la lubricación adecuados ayudan a disipar el calor y reducir la fricción, lo que prolonga la vida útil de la herramienta.
- Material de la herramienta: El material del que está hecha la herramienta de corte afecta su resistencia al desgaste. Materiales como el carburo y la cerámica ofrecen una excelente resistencia al desgaste.
- Geometría de la herramienta: La geometría de la herramienta de corte, incluido el ángulo de ataque, el ángulo de alivio y el diseño del rompevirutas, desempeña un papel importante en los patrones de desgaste.
- Material de la pieza de trabajo: El tipo de material que se mecaniza afecta el desgaste de la herramienta. Los materiales abrasivos pueden provocar un desgaste más rápido de las herramientas.
Procesos de mecanizado de precisión
Los procesos de mecanizado de precisión son métodos mediante los cuales las materias primas se transforman en piezas de alta precisión con tolerancias estrictas y acabados superficiales excepcionales. En esta sección, exploraremos cinco procesos clave de mecanizado de precisión: torneado, fresado, taladrado, rectificado y mecanizado por descarga eléctrica (EDM). Cada uno de estos procesos tiene un propósito único y se emplea en función de los requisitos específicos de la pieza de trabajo.A. Girando
El torneado es un proceso de mecanizado que se utiliza principalmente para dar forma a piezas cilíndricas. Implica rotar una pieza de trabajo mientras una herramienta de corte de un solo punto elimina material de la superficie exterior. Estos son los aspectos clave del torneado:- Piezas cilíndricas: El torneado es ideal para producir componentes cilíndricos como ejes, pasadores y manguitos.
- Simetría rotacional: Es muy adecuado para piezas que requieren simetría rotacional, ya que la pieza de trabajo gira en un torno mientras la herramienta de corte le da forma.
- Varias operaciones: El torneado puede realizar varias operaciones, incluido el refrentado, el torneado (reducción del diámetro), el torneado cónico y el roscado.
- Corte de un solo punto: Una sola herramienta de corte elimina material en un movimiento continuo, lo que resulta en una eliminación de material eficiente.
- Máquinas de torno: Tanto las máquinas de torno manuales como las controladas por CNC se utilizan comúnmente para operaciones de torneado.
B. Fresado
El fresado es un proceso de mecanizado de precisión versátil que emplea herramientas de corte multipunto para eliminar material de una pieza de trabajo. Es muy adecuado para crear una amplia gama de formas y características. Los aspectos clave de la molienda incluyen:- Versatilidad: El fresado puede producir superficies planas, ranuras, cavidades y contornos complejos. Se utiliza tanto para mecanizado 2D como 3D.
- Corte multipunto: Múltiples filos de corte en la herramienta interactúan con la pieza de trabajo simultáneamente, lo que permite una eliminación eficiente del material.
- Tipos de Fresado: El fresado se puede realizar utilizando varios tipos de cortadores, incluidos fresas de extremo, fresas de planear y molinos de bolas.
- Centros de mecanizado CNC: Las fresadoras controladas por CNC ofrecen un control preciso sobre el movimiento de la herramienta y se utilizan ampliamente en el mecanizado moderno.
- Altas velocidades: El fresado se puede realizar a altas velocidades, lo que permite una producción eficiente.
C. Perforación
La perforación es un proceso de mecanizado de precisión que se utiliza para crear agujeros en piezas de trabajo. Es una operación fundamental en diversas industrias. Los aspectos clave de la perforación incluyen:- Creación de agujeros: Las máquinas perforadoras utilizan herramientas especializadas llamadas taladros para eliminar material y crear orificios de diámetros específicos.
- Tipos de taladros: Hay diferentes tipos de brocas disponibles, incluidas brocas helicoidales, brocas centrales y brocas indexables, cada una diseñada para aplicaciones específicas.
- Exactitud: El posicionamiento y la alineación precisos son esenciales al perforar para garantizar que los orificios se creen con precisión.
- Velocidad y tasa de avance: Los parámetros de perforación, como la velocidad de rotación y el avance, son fundamentales para lograr las dimensiones de orificio deseadas.
- Refrigerante y Lubricación: Se utilizan refrigerante y lubricación adecuados para disipar el calor y reducir la fricción durante la perforación.
D. Molienda
El rectificado es un proceso de mecanizado de precisión que emplea muelas abrasivas para eliminar material y lograr tolerancias y acabados superficiales extremadamente ajustados. Los aspectos clave de la molienda incluyen:- Precisión excepcional: El rectificado puede alcanzar una precisión a nivel de micras, lo que lo hace ideal para aplicaciones que requieren la mayor precisión.
- Acabado de la superficie: Produce acabados superficiales superiores, eliminando a menudo la necesidad de procesos de acabado adicionales.
- Materiales: El rectificado es adecuado para materiales duros y abrasivos, incluidos acero endurecido, cerámica y carburos.
- Variedad de métodos de molienda: Los diferentes tipos de rectificadoras, como las rectificadoras de superficie, las rectificadoras cilíndricas y las rectificadoras sin centros, satisfacen diversas necesidades de mecanizado.
- Refrigerante: El refrigerante adecuado es esencial al rectificar para evitar el sobrecalentamiento y mantener la integridad de la rueda.
E. Mecanizado por descarga eléctrica (EDM)
EDM, o mecanizado por descarga eléctrica, es un proceso de mecanizado de precisión no tradicional que utiliza descargas eléctricas para eliminar material. Es especialmente adecuado para mecanizar formas complejas e intrincadas, así como materiales duros y resistentes al calor. Los aspectos clave de la electroerosión incluyen:- Mecanizado sin contacto: La electroerosión no implica contacto directo entre la herramienta y la pieza de trabajo, lo que reduce el riesgo de desgaste y daños de la herramienta.
- Alta precisión: La electroerosión puede lograr una alta precisión, lo que la hace adecuada para aplicaciones donde las tolerancias estrictas son esenciales.
- Formas complejas: Destaca en el mecanizado de formas complejas, troqueles, moldes y componentes con detalles finos.
- Electroerosión por hilo y electroerosión por plomo: Hay dos tipos principales de máquinas de electroerosión: electroerosión por hilo, que utiliza un electrodo de alambre, y electroerosión por plomo, que utiliza un electrodo moldeado.
- Proceso lento: La electroerosión es relativamente lenta en comparación con otros métodos de mecanizado, lo que la hace más adecuada para trabajos de baja cantidad y alta precisión.
Tolerancias y Control de Calidad
El mecanizado de precisión exige una atención meticulosa a los detalles y un compromiso riguroso con el control de calidad para garantizar que las piezas cumplan con los estándares especificados. En esta sección, exploraremos tres aspectos críticos del control de calidad en el mecanizado de precisión: dimensionamiento y tolerancias geométricas (GD&T), control estadístico de procesos (SPC) y garantía de calidad.A. Dimensionamiento y tolerancias geométricas (GD&T)
El dimensionamiento y tolerancias geométricos, a menudo abreviado como GD&T, es un sistema que se utiliza para definir y comunicar las variaciones permitidas en tamaño, forma, orientación y ubicación de características en una pieza. GD&T es vital en el mecanizado de precisión por las siguientes razones:- Comunicación precisa: GD&T proporciona un lenguaje estandarizado para que ingenieros, diseñadores y maquinistas comuniquen con precisión la intención del diseño y los requisitos dimensionales.
- Aclaración de tolerancia: Ayuda a definir la variación aceptable en las dimensiones críticas, asegurando que todas las partes interesadas comprendan las desviaciones permitidas.
- Calidad mejorada: GD&T promueve una mejor calidad al reducir la ambigüedad en las especificaciones de diseño, minimizando el riesgo de errores durante el mecanizado.
- Eficiencia de costo: Las especificaciones claras de GD&T pueden reducir los costos de fabricación, ya que es menos probable que las piezas sean desechadas o requieran reelaboración debido a malentendidos o interpretaciones erróneas.
- geometría compleja: Es particularmente útil para piezas con geometrías complejas, ya que garantiza que todas las funciones se fabriquen según las especificaciones deseadas.
B. Control estadístico de procesos (SPC)
El Control Estadístico de Procesos (SPC) es una metodología de control de calidad que utiliza técnicas estadísticas para monitorear y controlar el proceso de mecanizado. El SPC es esencial en el mecanizado de precisión por las siguientes razones:- Supervisión del proceso: SPC ayuda a monitorear los procesos de mecanizado en tiempo real, identificando variaciones o desviaciones de los parámetros deseados.
- Detección temprana de problemas: Al monitorear continuamente el proceso, SPC permite la detección temprana de problemas que podrían conducir a piezas fuera de especificaciones, lo que reduce el desperdicio y el retrabajo.
- Toma de decisiones basada en datos: SPC se basa en datos y análisis estadísticos para tomar decisiones informadas sobre los ajustes del proceso, asegurando que el proceso de mecanizado permanezca dentro de límites aceptables.
- Consistencia mejorada: SPC promueve la coherencia del proceso y reduce la probabilidad de producir piezas no conformes.
- Reducción de desperdicios y retrabajos: Al identificar y abordar las variaciones del proceso con prontitud, SPC minimiza la producción de piezas defectuosas, reduciendo los costos de desperdicio y retrabajo.
C. Garantía de calidad en el mecanizado de precisión
El aseguramiento de la calidad en el mecanizado de precisión abarca un enfoque integral para garantizar que las piezas fabricadas cumplan o superen los estándares de calidad especificados. Implica varios elementos, entre ellos:- Documentación del proceso: La documentación detallada de los procesos de mecanizado, incluidos los procedimientos operativos estándar (POE) y las instrucciones de trabajo, garantiza que cada paso se realice de forma coherente.
- Inspección y Medición: La inspección y medición rigurosas utilizando instrumentos de precisión y técnicas de metrología verifican que las piezas cumplan con las tolerancias y estándares de calidad especificados.
- Calibración: La calibración periódica de equipos de mecanizado e instrumentos de medición es esencial para mantener la precisión y la trazabilidad.
- Verificación de materiales: La verificación de las propiedades, composición y calidad del material es fundamental para garantizar que el material utilizado cumpla con los requisitos de diseño.
- Formación de los empleados: Los programas de capacitación y desarrollo de habilidades para maquinistas y personal de control de calidad garantizan que sean competentes en sus funciones y responsabilidades.
- Análisis de la causa raíz: Cuando se identifican piezas no conformes, se realiza un análisis de la causa raíz para determinar el origen del problema e implementar acciones correctivas.
- Mejora continua: Una cultura de mejora continua fomenta la innovación e impulsa mejoras continuas en los procesos de mecanizado y los procedimientos de control de calidad.
- Comentarios: Recopilar y analizar los comentarios de los clientes ayuda a identificar áreas de mejora y alinea los procesos de mecanizado con las expectativas del cliente.
Conclusión
A. El arte y la ciencia del mecanizado de precisión
El mecanizado de precisión se encuentra en la intersección del arte y la ciencia, donde la creatividad, la habilidad y la innovación convergen para producir piezas de alta precisión que impulsan las industrias y dan forma al mundo moderno. Es a la vez una forma de arte, que requiere la habilidad y la experiencia de maquinistas que transforman las materias primas en obras de excelencia de ingeniería, y una ciencia que se basa en tecnología de punta, ciencia de materiales y procesos avanzados para lograr una precisión incomparable. El viaje del mecanizado de precisión nos lleva a través de la comprensión de los materiales y sus propiedades, el dominio de las herramientas y maquinaria de corte y el control meticuloso de los procesos y tolerancias. Abarca el lenguaje del dimensionamiento y tolerancias geométricos, la vigilancia del control estadístico de procesos y el compromiso con el aseguramiento de la calidad. El mecanizado de precisión desempeña un papel fundamental en diversas industrias, desde la aeroespacial y la automotriz hasta los dispositivos médicos y la electrónica, dando forma a todo, desde motores de aviones hasta articulaciones artificiales y microchips. Permite la creación de componentes que funcionan con una precisión y confiabilidad inigualables, a menudo superando los límites de lo posible.B. Pensamientos finales
Al concluir esta exploración del mecanizado de precisión, queda claro que este campo no se trata sólo de la creación de piezas; se trata de la creación de posibilidades. La búsqueda de la precisión impulsa la innovación, ampliando los límites de lo que se puede lograr. Ya sea la delicada artesanía necesaria para crear los intrincados engranajes de un reloj o la tecnología avanzada necesaria para fabricar componentes aeroespaciales complejos, el mecanizado de precisión es el núcleo de todo. El futuro del mecanizado de precisión es prometedor. Los avances en la ciencia de los materiales, la automatización y las tecnologías digitales continúan remodelando el panorama. La miniaturización, la impresión 3D y las prácticas de fabricación sostenible son cada vez más prominentes, lo que abre nuevos horizontes para la industria. En un mundo donde la precisión importa más que nunca, el mecanizado de precisión sigue siendo un pilar indispensable de la ingeniería moderna. Es un testimonio del ingenio humano y de nuestra inquebrantable búsqueda de la excelencia en cada faceta de la fabricación. A medida que crece la demanda de mayor precisión y componentes más complejos, el mecanizado de precisión seguirá evolucionando, enfrentando los desafíos del mañana con la misma dedicación y precisión que lo han definido durante siglos.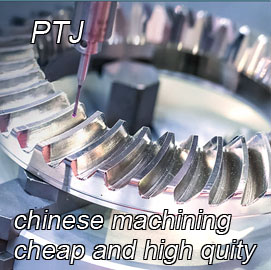
Servicios
- Mecanizado de 5 ejes
- Fresado CNC
- Torneado CNC
- Industrias de mecanizado
- Proceso de mecanizado
- Tratamiento de superficies
- Mecanizado de metales
- Mecanizado de plástico
- Molde de pulvimetalurgia
- Die Casting
- Galería de piezas
Casos de Estudio
- Auto partes de metal
- Partes de maquinaria
- Disipador de calor LED
- Piezas de construcción
- Partes móviles
- Partes médicas
- Componentes electrónicos
- Mecanizado a medida
- Partes de la bicicleta
Lista de materiales
- Mecanizado de aluminio
- Mecanizado de titanio
- Mecanizado de acero inoxidable
- Mecanizado de cobre
- Mecanizado de latón
- Mecanizado de súper aleación
- Mecanizado de Peek
- Mecanizado UHMW
- Unilate Mecanizado
- Mecanizado PA6
- Mecanizado PPS
- Mecanizado de teflón
- Mecanizado de Inconel
- Mecanizado de acero para herramientas
- Más material
Galería de piezas