Una guía completa sobre cómo configurar una herramienta de corte de torno
Configurar una herramienta de corte de torno es una habilidad fundamental para cualquier maquinista, especialmente cuando se trata de tornos de control numérico por computadora (CNC). La configuración adecuada de la herramienta es crucial para lograr resultados de mecanizado precisos y exactos. En esta guía completa, profundizaremos en los intrincados detalles de cómo configurar una herramienta de corte de torno para torneado CNC. Desde los conceptos básicos de los componentes de las herramientas de torno hasta técnicas avanzadas para optimizar el rendimiento de corte, este artículo tiene como objetivo proporcionar una comprensión integral del proceso. Al final de esta guía, tendrá el conocimiento y las habilidades necesarias para configurar una herramienta de corte de torno con confianza y precisión, garantizando resultados óptimos en sus operaciones de torneado CNC.
Comprensión de las herramientas de corte de torno
En el mundo del mecanizado, las herramientas de corte de torno son componentes indispensables para dar forma y transformar materias primas en piezas de ingeniería de precisión. Ya sea que esté trabajando con tornos manuales tradicionales o máquinas de torneado CNC avanzadas, es esencial tener un conocimiento profundo de las herramientas de corte de torno. En este apartado profundizaremos en las características, funciones y tipos de herramientas de corte en torno.
Características de las herramientas de corte de torno
Las herramientas de corte de torno están diseñadas para realizar una variedad de operaciones de mecanizado, como torneado, refrentado, ranurado, roscado y más. Estas herramientas comparten varias características comunes:
- Dureza: Las herramientas de corte de torno suelen estar hechas de acero de alta velocidad (HSS), carburo u otros materiales de herramientas especializados. Estos materiales se eligen por su dureza, lo que permite que la herramienta resista las altas temperaturas y presiones generadas durante el corte.
- Innovador: El filo de una herramienta de torno es la parte que realmente elimina el material de la pieza de trabajo. Está diseñado para ser afilado y preciso, y la geometría del filo puede variar según la tarea específica para la que esté destinada la herramienta.
- Caña: El vástago de la herramienta de torno es la pieza que se sujeta al portaherramientas. Proporciona estabilidad y rigidez a la herramienta durante el proceso de mecanizado. Los diseños de vástago pueden diferir según el tipo de herramienta y las especificaciones del fabricante.
- Portaherramientas: El portaherramientas es un componente crucial, especialmente en el torneado CNC, ya que sujeta de forma segura la herramienta de torno en su lugar. Debe proporcionar estabilidad, precisión y facilidad de ajuste para garantizar un rendimiento óptimo de la herramienta.
- Geometría: La geometría de la herramienta de corte, incluido el ángulo de ataque, el ángulo libre y el rompevirutas, desempeña un papel importante a la hora de determinar el rendimiento de la herramienta. La geometría adecuada es esencial para lograr una eliminación de material y una evacuación de virutas eficientes.
- Para el apanado: Muchas herramientas de corte de torno vienen con recubrimientos especializados, como TiN (nitruro de titanio) o TiAlN (nitruro de titanio y aluminio), para mejorar la vida útil de la herramienta, reducir la fricción y mejorar el rendimiento.
Funciones de las herramientas de corte de torno
Las herramientas de corte del torno realizan varias funciones fundamentales en el proceso de mecanizado:
- Eliminación de materiales: La función principal de las herramientas de corte de torno es eliminar material de una pieza de trabajo. Esta eliminación puede ocurrir mediante torneado (rotación de la pieza de trabajo mientras se corta), refrentado (creación de una superficie plana) u otras operaciones.
- Control dimensional: Las herramientas de corte son las encargadas de garantizar que las dimensiones de la pieza mecanizada coincidan con las especificaciones deseadas. El control preciso es esencial para lograr resultados precisos y consistentes.
- Acabado de la superficie: La calidad del acabado superficial está determinada por el filo de la herramienta de corte, la geometría y los parámetros de corte utilizados. Una herramienta de corte bien mantenida y configurada correctamente contribuye a un acabado superficial suave y fino.
- Control de virutas: El control eficaz de las virutas es esencial para prevenir la acumulación de virutas y mantener un entorno de trabajo limpio y seguro. El rompevirutas de algunas herramientas ayuda a facilitar la eliminación de virutas.
- Eficiencia: Las herramientas de corte de torno están diseñadas para hacer que los procesos de mecanizado sean eficientes y rentables. Ayudan a minimizar el desperdicio de material y optimizar la vida útil de la herramienta, reduciendo los costos de producción.
Tipos de herramientas de corte de torno
Las herramientas de corte de torno están disponibles en una variedad de tipos, cada una adaptada a tareas de mecanizado específicas. A continuación se muestran algunos tipos comunes:
- Herramientas de torneado: Estas herramientas son versátiles y se utilizan para operaciones de torneado cilíndrico. Pueden dar forma a las superficies externas e internas de una pieza de trabajo.
- Herramientas aburridas: Se emplean herramientas perforadoras para agrandar o terminar los agujeros existentes. Están diseñados para brindar precisión y exactitud en el mecanizado de agujeros.
- Herramientas de despedida: Las herramientas de separación se utilizan para separar una pieza de trabajo de un material más grande. Crean líneas de separación definidas con un desperdicio mínimo.
- Herramientas de roscado: Las herramientas de roscado se utilizan para cortar hilos en una pieza de trabajo. Vienen en varias formas y tamaños para diferentes requisitos de roscado.
- Herramientas de ranurado: Las herramientas de ranurado crean ranuras o huecos en una pieza de trabajo, generalmente para acomodar juntas tóricas, anillos de retención u otras características.
- Herramientas de revestimiento: Las herramientas de refrentado están diseñadas para crear superficies planas en el extremo de una pieza de trabajo. A menudo se utilizan para lograr superficies perpendiculares o eliminar material del extremo de una pieza de trabajo.
Comprender las características y funciones de las herramientas de corte de torno es esencial para seleccionar la herramienta adecuada para una tarea de mecanizado específica. La elección de la herramienta de corte puede afectar significativamente la calidad y eficiencia del proceso de mecanizado, lo que la convierte en una decisión crítica en cualquier operación de torno. Además, el mantenimiento y la configuración de las herramientas adecuados son vitales para garantizar resultados consistentes y precisos, que se analizarán con más detalle más adelante en esta guía.
Tipos de herramientas de corte de torno
Las herramientas de corte de torno vienen en varios tipos, cada una diseñada específicamente para una tarea de mecanizado particular. Comprender estos diferentes tipos de herramientas de corte y sus aplicaciones es esencial para seleccionar la herramienta adecuada para un trabajo determinado. A continuación se muestran algunos tipos comunes de herramientas de corte de torno:
Herramientas de torneado:
- Herramienta de punta redonda: Se utiliza para operaciones de torneado de uso general. Cuenta con un filo redondeado y es adecuado tanto para cortes de desbaste como de acabado.
- Herramienta de diamante: Llamado así por su filo en forma de diamante, es ideal para el mecanizado preciso de diversos materiales, incluidos metales y plásticos.
- Herramienta de punta cuadrada: Presenta un filo de corte cuadrado y generalmente se usa para operaciones de refrentado y torneado de escuadras.
Herramientas aburridas:Barra de taladro interno: Se utiliza para ampliar y terminar agujeros existentes en una pieza de trabajo. Está diseñado para brindar precisión y puede crear dimensiones internas precisas.
Herramientas de despedida:Hoja de despedida: Estas herramientas se utilizan para cortar una pieza de trabajo de un stock más grande. Crean una línea de separación definida con un desperdicio mínimo.
Herramientas de roscado:
- Herramienta para cortar hilos: Diseñado para crear roscas externas en una pieza de trabajo. Vienen en varias formas y tamaños para diferentes requisitos de roscado.
- Herramienta de seguimiento de hilos: Se utiliza para perseguir o restaurar hilos existentes. Estas herramientas se utilizan comúnmente para reparar roscas.
Herramientas de ranurado:Herramienta de ranurado: Estas herramientas crean ranuras o huecos en una pieza de trabajo, a menudo para acomodar juntas tóricas, anillos de retención u otras características.
Herramientas de revestimiento:Herramienta de revestimiento: Se utiliza para crear superficies planas al final de una pieza de trabajo. A menudo se utiliza para lograr superficies perpendiculares o eliminar material del extremo de una pieza de trabajo.
Herramientas de tronzado y ranurado:Herramienta combinada: Estas herramientas versátiles están diseñadas para operaciones de tronzado y ranurado, lo que ahorra tiempo y cambios de herramientas.
Herramientas de roscado y ranurado:Herramienta combinada de roscado y ranurado: Ideal para trabajos que requieren operaciones de roscado y ranurado en la misma pieza de trabajo.
Herramientas de biselado:Herramienta de biselado: Se utiliza para crear chaflanes o bordes biselados en la pieza de trabajo. Los chaflanes se aplican a menudo para mejorar la apariencia y la facilidad de montaje de piezas mecanizadas.
Herramientas de moleteado:Herramienta moleteadora: El moleteado es un proceso de creación de un patrón texturizado en una pieza de trabajo, generalmente para mejorar el agarre o la estética. Las herramientas de moleteado vienen en varios patrones y diseños.
Herramientas de formación:Herramienta de formulario: Estas herramientas están diseñadas a medida para geometrías de piezas específicas y se utilizan a menudo para producir formas complejas y no estándar.
Herramientas especiales:Herramientas de perfil: Se utiliza para crear perfiles complejos en una pieza de trabajo.
Herramientas de refrentado y torneado: Están diseñados tanto para operaciones de refrentado como de torneado.
Herramientas de corte: Diseñado para cortar la pieza de trabajo para crear piezas separadas o eliminar el exceso de material.
La selección de la herramienta de corte adecuada depende de factores como el material que se mecaniza, el acabado deseado, las dimensiones requeridas y la operación específica que se realiza. Es fundamental elegir la herramienta adecuada y mantenerla adecuadamente para garantizar un mecanizado eficiente y preciso. La selección adecuada de herramientas, junto con la configuración y el ajuste correctos, es crucial para lograr resultados de alta calidad en las operaciones de torno.
Componentes de una herramienta de corte de torno
Una herramienta de corte de torno es un instrumento de precisión diseñado para dar forma, cortar y eliminar material de una pieza de trabajo. Para comprender cómo funciona y cómo configurarlo correctamente, es fundamental estar familiarizado con sus distintos componentes. Estos son los componentes clave de una herramienta de corte de torno:
- Portaherramientas:El portaherramientas es la pieza que asegura la herramienta de corte en su lugar. Se fija al poste de herramientas del torno y proporciona la rigidez y estabilidad necesarias para las operaciones de mecanizado. Los portaherramientas vienen en varios diseños para adaptarse a diferentes tipos de herramientas de corte.
- Caña:El vástago es la parte de la herramienta de corte que encaja en el portaherramientas. Normalmente es cilíndrico y está sujeto de forma segura dentro del soporte. Las dimensiones y la forma del vástago pueden variar según el tipo y diseño de la herramienta.
- Innovador:El filo es la parte afilada de la herramienta que entra en contacto y elimina material de la pieza de trabajo. La calidad del filo y su geometría afectan significativamente el rendimiento de corte y el acabado superficial. Es fundamental mantener el filo y la precisión del filo.
- Insertar:Muchas herramientas de corte modernas utilizan insertos reemplazables, que normalmente están hechos de materiales duros como carburo o cerámica. Estos insertos tienen la geometría de corte y están asegurados en un bolsillo de la herramienta de corte. Se pueden rotar o reemplazar cuando se desgastan o dañan, lo que prolonga la vida útil de la herramienta.
- Nariz de herramienta:La punta de la herramienta es la punta de la herramienta de corte donde se unen el filo y el inserto (si se usa). La punta de la herramienta debe estar posicionada y alineada con precisión para un mecanizado preciso. Algunas herramientas de corte de torno tienen un radio de punta de herramienta ajustable para un mejor control sobre el rendimiento de la herramienta.
- Flanco de herramienta:El flanco de la herramienta es la superficie lateral de la herramienta de corte que no forma parte del filo. Los ángulos de incidencia adecuados en el flanco de la herramienta garantizan la evacuación de la viruta y reducen la fricción entre la herramienta y la pieza de trabajo.
- Cara de inclinación de la herramienta:La cara de inclinación es la superficie de la herramienta de corte que mira hacia la pieza de trabajo. El ángulo y la condición de la cara de desprendimiento afectan la formación de viruta y la eficiencia del proceso de corte. El ángulo de ataque es un aspecto crítico de la geometría de la herramienta.
- Ángulo de alivio de la herramienta:El ángulo de alivio es el ángulo entre el flanco de la herramienta y el eje de la herramienta. Garantiza que el filo no roce contra la pieza de trabajo, lo que reduce la fricción y la generación de calor.
- Ángulo de separación de herramientas:El ángulo libre es el ángulo entre la cara de inclinación y la superficie de la pieza de trabajo. Permite que las virutas fluyan suavemente y evita interferencias entre la herramienta y la pieza de trabajo.
- Rompevirutas (si corresponde):Algunas herramientas de corte, especialmente aquellas utilizadas para operaciones de desbaste, cuentan con un rompevirutas, una ranura o muesca en la cara de inclinación. El rompevirutas ayuda a controlar la formación de virutas y a mejorar la evacuación de virutas.
El montaje, la alineación y el mantenimiento adecuados de estos componentes son esenciales para lograr un mecanizado preciso y eficiente. La elección de la herramienta de corte y su configuración deben adaptarse a la operación de mecanizado específica y al material con el que se está trabajando. También son necesarios una inspección y un mantenimiento periódicos de los componentes de la herramienta de corte para garantizar resultados consistentes y de alta calidad.
Elección de la herramienta de corte adecuada para el trabajo
Seleccionar la herramienta de corte adecuada es una decisión crítica en cualquier operación de mecanizado, ya que influye en gran medida en la calidad, eficiencia y precisión del trabajo. Se deben considerar varios factores al elegir la herramienta de corte adecuada para un trabajo específico. A continuación le ofrecemos una guía sobre cómo elegir la herramienta de corte adecuada para su proyecto de mecanizado:
1. Material de la pieza de trabajo:
El material que está mecanizando es uno de los factores más críticos en la selección de herramientas. Los diferentes materiales tienen diferente dureza, conductividad térmica y abrasividad. Considera lo siguiente:
- Dureza: Los materiales duros como el acero endurecido o la cerámica requieren herramientas de corte con filos duros, como insertos de carburo, para soportar las altas fuerzas de corte.
- Materiales blandos: Para materiales más blandos como el aluminio o los plásticos, el acero rápido (HSS) u otros materiales para herramientas pueden ser suficientes.
2. Operación de mecanizado:
La operación específica que esté realizando, como tornear, fresar, taladrar, roscar o ranurar, determinará el tipo de herramienta de corte que necesita. Se diseñan diferentes herramientas para diversas tareas y elegir la adecuada garantiza un rendimiento óptimo.
3. Velocidad de corte y avance:
Determine la velocidad de corte y el avance requeridos según el material y la operación de mecanizado. Los fabricantes de herramientas de corte brindan recomendaciones para estos parámetros según el diseño de la herramienta y el material que se está mecanizando. Cumplir con estas recomendaciones es crucial para lograr los resultados deseados.
4. Geometría de la herramienta:
Considere la geometría de la herramienta de corte, incluido el ángulo de ataque, el ángulo libre y el radio de la punta de la herramienta. La geometría de la herramienta debe coincidir con el material y el tipo de corte. Por ejemplo, un ángulo de incidencia positivo es adecuado para materiales más blandos, mientras que un ángulo de incidencia negativo es mejor para materiales más duros.
5. Dimensiones de la pieza de trabajo:
El tamaño y las dimensiones de la pieza de trabajo también influyen en la selección de la herramienta. Algunas herramientas de corte son más adecuadas para operaciones de desbaste para eliminar material a granel rápidamente, mientras que otras están diseñadas para acabado para lograr dimensiones y acabados superficiales precisos.
6. Requisitos de acabado superficial:
Si necesita un acabado superficial específico, seleccione una herramienta de corte con la geometría y el filo adecuados. Las herramientas de acabado están diseñadas para proporcionar un acabado superficial más suave, mientras que las herramientas de desbaste son más eficientes para la eliminación de material.
7. Material de la herramienta:
La elección del material de la herramienta es crucial. Las herramientas de carburo, acero de alta velocidad (HSS), cerámica y recubiertas tienen sus ventajas y limitaciones. Considere factores como la vida útil de la herramienta, la resistencia al desgaste y el costo del material de la herramienta en su decisión.
8. Refrigerante y Lubricación:
Considere si la operación de corte requiere refrigerante o lubricación. Algunos materiales generan calor excesivo durante el mecanizado y el uso del refrigerante o lubricante adecuado puede prolongar la vida útil de la herramienta y mejorar el rendimiento de corte.
9. Recubrimientos de herramientas:
Muchas herramientas de corte modernas vienen con recubrimientos especializados como TiN (nitruro de titanio) o TiAlN (nitruro de titanio y aluminio) para mejorar la resistencia al desgaste y reducir la fricción. Elija una herramienta con un recubrimiento adecuado para su aplicación específica.
10. Consideraciones de costos:
Es fundamental equilibrar el coste de la herramienta de corte con su rendimiento y longevidad. Si bien las herramientas premium pueden ofrecer una vida útil más larga y un mejor rendimiento, es esencial encontrar un equilibrio que se ajuste al presupuesto de su proyecto.
11. Compatibilidad entre portaherramientas y máquinas:
Asegúrese de que la herramienta de corte elegida sea compatible con el sistema portaherramientas de su torno o centro de mecanizado. El portaherramientas debe proporcionar estabilidad y rigidez a la herramienta de corte durante el proceso de mecanizado.
En última instancia, la herramienta de corte adecuada para el trabajo dependerá de una combinación de estos factores. Consulte siempre las recomendaciones del fabricante de la herramienta y considere buscar asesoramiento de maquinistas experimentados o expertos en herramientas si no está seguro. La selección y configuración adecuadas de las herramientas son fundamentales para lograr resultados de mecanizado eficientes y precisos.
Configuración de la herramienta de corte de torno
La configuración de una herramienta de corte de torno para torneado CNC es un proceso sistemático que implica varios pasos cruciales. Cada paso es vital para garantizar que la herramienta de corte esté correctamente posicionada y alineada, lo que en última instancia conduce a un mecanizado preciso y eficiente. Repasemos el proceso paso a paso:
Paso 1: Preparación del torno y la pieza de trabajo
Antes de poder configurar la herramienta de corte, es fundamental preparar tanto el torno como la pieza de trabajo:
- Asegure la pieza de trabajo: Asegúrese de que la pieza de trabajo esté sujeta firmemente en el portabrocas o la pinza del torno. Asegúrese de que gire suavemente sin tambalearse ni vibrar.
- Seguridad: Asegúrese de que se implementen todas las medidas de seguridad, incluido el uso de equipo de protección personal (EPP) adecuado y la configuración correcta del torno.
Paso 2: Seleccionar el portaherramientas correcto
El portaherramientas es un componente crítico en el proceso de configuración. Elija el portaherramientas adecuado en función de factores como el tipo de herramienta de corte, la operación que se realiza y el sistema de poste de herramientas del torno.
- Haga coincidir el portaherramientas con la herramienta de corte: Asegúrese de que el portaherramientas sea compatible con el tipo y tamaño de la herramienta de corte que desea utilizar.
- Rigidez del portaherramientas: Elija un portaherramientas que proporcione estabilidad y rigidez. Esto es especialmente importante en aplicaciones de alta precisión.
Paso 3: montar la herramienta de corte
El montaje de la herramienta de corte implica asegurarla en el portaherramientas y asegurarse de que esté firme y correctamente posicionada:
- Asegure la herramienta de corte: Inserte la herramienta de corte en el portaherramientas y apriete cualquier mecanismo de sujeción, como tornillos de fijación o pinzas. Asegúrese de que la herramienta esté sujeta de forma segura.
- Orientación: Verifique que la herramienta de corte esté orientada correctamente con respecto a la pieza de trabajo. La herramienta debe colocarse para enganchar la pieza de trabajo en el ángulo y profundidad deseados.
Paso 4: Ajuste de la altura de la herramienta y la alineación de la línea central
La altura correcta de la herramienta y la alineación de la línea central son cruciales para lograr dimensiones de mecanizado precisas:
- Ajuste de altura de la herramienta: Ajuste la altura de la herramienta para alinearla con la línea central del husillo del torno. Utilice un medidor de altura de herramienta o una barra de prueba para colocar la herramienta a la altura correcta.
- Alineación de la línea central: Asegúrese de que la herramienta esté alineada con la línea central del husillo del torno. La desalineación puede provocar un mecanizado descentrado, lo que afecta la precisión de la pieza.
Paso 5: Configuración de la compensación del radio de la punta de la herramienta
Para el torneado CNC, la compensación del radio de la punta de la herramienta tiene en cuenta la geometría de la herramienta de corte. Esto es particularmente importante cuando se utilizan herramientas de inserción:
- Determine el radio de la punta de la herramienta: Mida o busque el radio exacto de la punta del inserto de herramienta de corte que está utilizando.
- Ingrese el valor del radio: En el software de control CNC, ingrese el valor medido del radio de la punta de la herramienta para garantizar que la máquina compense la geometría de la herramienta durante el mecanizado.
Paso 6: Configuración de compensaciones de herramientas
Las compensaciones de herramientas tienen en cuenta las variaciones en las dimensiones de la herramienta y la geometría de la pieza de trabajo. Garantizan que la posición de la herramienta se ajuste con precisión para el mecanizado:
- Seleccione la compensación de herramienta correcta: Determine el valor de compensación de herramienta apropiado según la geometría de la herramienta y la operación de mecanizado. Este valor de compensación compensa cualquier discrepancia.
- Introduzca valores de compensación: Introduzca los valores de compensación elegidos en el software de control CNC. Estos valores indicarán a la máquina cómo ajustar la posición de la herramienta con precisión.
Durante todo el proceso de configuración de la herramienta, utilice instrumentos de medición de precisión como micrómetros, medidores de altura e indicadores de cuadrante para verificar y ajustar la alineación de la herramienta. Inspeccione y mantenga periódicamente la herramienta de corte para garantizar que permanezca afilada y en buenas condiciones, ya que una herramienta bien mantenida contribuye a obtener resultados de mecanizado consistentes y precisos.
Configurar correctamente la herramienta de corte del torno en estos pasos es crucial para lograr resultados óptimos en las operaciones de torneado CNC. La precisión y la atención al detalle durante la configuración de la herramienta son factores clave en la producción de piezas mecanizadas de alta calidad.
Optimización de los parámetros de corte para torneado CNC
La optimización de los parámetros de corte es esencial para lograr operaciones de torneado CNC eficientes y de alta calidad. Los cuatro aspectos clave a considerar al optimizar los parámetros de corte son las velocidades y avances, la profundidad de corte, los fluidos y lubricantes de corte y la gestión de la vida útil de la herramienta.
1. Velocidades y avances:
- a. Velocidad de corte (velocidad superficial):La velocidad de corte, a menudo denominada velocidad superficial, es la velocidad a la que interactúan la pieza de trabajo y la herramienta de corte. Se mide en pies de superficie por minuto (SFM) o metros por minuto (m/min). Para optimizar la velocidad de corte, considere el material que se está mecanizando y el material de la herramienta. Las herramientas de acero de alta velocidad (HSS) tienen velocidades de corte recomendadas más bajas que las herramientas de carburo, por ejemplo. Consulte los datos del fabricante de la herramienta o los manuales de mecanizado para determinar las velocidades de corte recomendadas para materiales y herramientas específicos.
- b. Tasa de alimentación:La velocidad de avance es la velocidad lineal a la que la herramienta de corte avanza hacia la pieza de trabajo. Se mide en pulgadas por revolución (IPR) o milímetros por revolución (mm/rev). Para optimizar la velocidad de avance, considere factores como las propiedades del material, la geometría de la herramienta y el acabado superficial deseado. Las velocidades de avance más altas generalmente son más productivas, pero pueden requerir herramientas más resistentes.
- C. Relación entre velocidad de corte y avance:Equilibrar la velocidad de corte y el avance es crucial para una eliminación eficiente del material. Un aumento en la velocidad de corte generalmente permite una velocidad de avance más alta, pero ambas deben ajustarse juntas para evitar el desgaste y el sobrecalentamiento de la herramienta.
2. Profundidad de corte:
- a. Profundidad de corte (DOC):La profundidad de corte es la distancia que penetra la herramienta de corte en la pieza de trabajo. Es fundamental considerar el material y las capacidades de la herramienta. Optimice la profundidad de corte en función de la dureza del material y la resistencia y rigidez de la herramienta. Es posible que sean necesarios cortes superficiales para materiales más duros, mientras que se pueden lograr cortes más profundos en materiales más blandos.
- b. Profundidad de corte axial y radial:En el torneado CNC, considere la profundidad de corte tanto axial (a lo largo de la pieza de trabajo) como radial (a lo largo del diámetro de la pieza de trabajo). Las profundidades óptimas para cada uno variarán según la operación y el material.
3. Fluidos y lubricantes de corte:
- a. Seleccionar el fluido de corte adecuado:Los fluidos de corte son esenciales para disipar el calor, reducir la fricción y mejorar la evacuación de virutas. Elija el fluido de corte adecuado según el material y la operación de mecanizado. Es posible que se prefieran refrigerantes solubles en agua, refrigerantes a base de aceite mineral o sintéticos para diferentes materiales.
- b. Aplicación adecuada:Aplique fluidos de corte de manera efectiva al área de corte para garantizar una lubricación y enfriamiento adecuados. Esto se puede hacer mediante enfriamiento por inundación, sistemas de nebulización o suministro de refrigerante a través de la herramienta, según las capacidades de la máquina.
- C. Monitoreo y Mantenimiento:Supervise periódicamente los niveles, el estado y la contaminación del líquido de corte para garantizar que sigan siendo eficaces. Mantenga los sistemas de fluidos de corte para evitar problemas como el crecimiento y la degradación bacteriana.
4. Gestión de la vida útil de las herramientas:
- a. Inspección y mantenimiento de herramientas:Implementar un programa de mantenimiento e inspección de herramientas de rutina para garantizar que las herramientas estén en buenas condiciones. Las herramientas desafiladas o dañadas pueden provocar una mala calidad del mecanizado y una vida útil reducida.
- b. Calendario de reemplazo de herramientas:Establezca un cronograma de reemplazo de herramientas basado en factores como el desgaste de las herramientas, el tiempo de actividad de la máquina y los requisitos de producción. Esto ayuda a prevenir fallos inesperados en las herramientas y a mantener una calidad de mecanizado constante.
- C. Optimización de la vida útil de la herramienta:Algunos materiales y recubrimientos para herramientas ofrecen una vida útil más larga. Considere el uso de herramientas de alto rendimiento para optimizar la vida útil de la herramienta y reducir el tiempo de inactividad de la producción.
- d. Control de virutas de herramientas:Un control eficaz de la viruta, incluido el uso de rompevirutas y una geometría adecuada de la herramienta, puede prolongar la vida útil de la herramienta al reducir el desgaste inducido por la viruta.
La optimización de los parámetros de corte en el torneado CNC es un proceso continuo. Es posible que sea necesario experimentar y realizar ajustes para encontrar los mejores parámetros para una aplicación específica. Supervise y ajuste periódicamente estos parámetros para garantizar un rendimiento de mecanizado, una vida útil de la herramienta y una calidad de las piezas óptimos. Los parámetros de corte adecuadamente optimizados no sólo mejoran la eficiencia del mecanizado sino que también reducen el desgaste de la herramienta y, en última instancia, los costos de producción.
Solución de problemas comunes en la configuración de herramientas
Solucionar problemas comunes en la configuración de herramientas es una habilidad esencial para los maquinistas y operadores de CNC. Comprender y abordar estos problemas puede ayudar a mantener la precisión y la calidad de las operaciones de mecanizado. A continuación se muestran algunos problemas comunes de configuración de herramientas y sus soluciones:
1. Charla de herramientas:
Edición: La vibración de la herramienta se produce cuando la herramienta de corte vibra durante el proceso de mecanizado, lo que provoca un acabado superficial deficiente, desgaste de la herramienta y posibles daños a la pieza de trabajo.
Solución:
- Reducir la velocidad o aumentar el avance: Ajuste los parámetros de corte disminuyendo la velocidad de corte o aumentando la velocidad de avance. Este cambio puede amortiguar las vibraciones y reducir el ruido.
- Verificar la rigidez de la herramienta: Asegúrese de que el portaherramientas y la herramienta estén correctamente asegurados y que la herramienta no sobresalga demasiado del portaherramientas.
- Comprobar la sujeción de la pieza de trabajo: Asegúrese de que la pieza de trabajo esté sujeta firmemente para evitar vibraciones relacionadas con la pieza de trabajo.
- Utilice técnicas de amortiguación: Algunas máquinas vienen con funciones para amortiguar las vibraciones. Si están disponibles, considere usarlos.
- Elija una herramienta más rígida: Una herramienta más rígida, como una con menos ranuras, puede ayudar a reducir la vibración.
2. Acabado superficial deficiente:
Edición: Un acabado superficial deficiente puede deberse a problemas con la configuración de la herramienta o los parámetros de corte, lo que genera superficies rugosas o inconsistentes en la pieza de trabajo.
Solución:
- Verificar la geometría de la herramienta: Asegúrese de que la geometría de la herramienta de corte sea adecuada para la operación. Una herramienta afilada con la geometría correcta es crucial para lograr un buen acabado superficial.
- Optimizar los parámetros de corte: Ajuste la velocidad de corte, la velocidad de avance y la profundidad de corte para encontrar la mejor combinación para el material y la operación específicos.
- Verifique el desgaste de las herramientas: Inspeccione la herramienta en busca de signos de desgaste o daños, como bordes desconchados. Reemplace o reafile la herramienta según sea necesario.
- Utilice el fluido de corte adecuado: La lubricación y el enfriamiento adecuados pueden afectar significativamente el acabado de la superficie. Utilice el fluido de corte adecuado para el material y la operación.
- Minimizar la vibración: Aborde los problemas de vibración para evitar crear irregularidades en la superficie.
3. Inexactitudes dimensionales:
Edición: Las piezas pueden tener dimensiones incorrectas debido a herramientas desalineadas o desgaste de herramientas.
Solución:
- Verifique la configuración de la herramienta: Verifique que la herramienta esté correctamente configurada con la altura y alineación correctas con respecto a la pieza de trabajo.
- Calibrar máquina: Asegúrese de que la máquina CNC esté calibrada correctamente y de que interprete con precisión las compensaciones y los datos de la herramienta.
- Ajustar compensaciones de herramientas: Corrija cualquier error en las compensaciones de herramientas midiendo con precisión la herramienta e ingresando los valores de compensación adecuados en el control CNC.
- Inspeccionar el desgaste de la herramienta: Inspeccione periódicamente la herramienta de corte en busca de desgaste y reemplácela o recúlela cuando sea necesario.
4. Problemas de control de chips:
Edición: Un control inadecuado de las virutas puede provocar problemas como obstrucción de las virutas, mala evacuación de las virutas y daños a la pieza de trabajo o a la herramienta.
Solución:
- Elija la geometría de herramienta adecuada: Seleccione una herramienta de corte con el rompevirutas o la geometría adecuada para el material y la operación.
- Optimizar los parámetros de corte: Ajuste las velocidades de avance, las velocidades de corte y las profundidades de corte para optimizar la formación y evacuación de virutas.
- Utilice una lubricación adecuada: El uso adecuado de los fluidos de corte puede ayudar a lubricar y facilitar la evacuación de virutas.
- Verifique la alineación de la herramienta y la pieza de trabajo: Asegúrese de que la herramienta esté correctamente alineada con la pieza de trabajo para evitar problemas relacionados con virutas.
5. Rotura de herramienta:
Edición: La rotura de la herramienta puede ocurrir debido a una fuerza excesiva, una configuración incorrecta de la herramienta o problemas relacionados con el material.
Solución:
- Optimizar los parámetros de corte: Reduzca las fuerzas de corte ajustando parámetros como velocidades de avance, velocidades de corte y profundidades de corte.
- Verifique la configuración de la herramienta: Asegúrese de que la herramienta esté montada de forma segura en el portaherramientas y que esté correctamente alineada.
- Utilice material de herramienta adecuado: Elija el material de herramienta adecuado para el material específico que está mecanizando. Por ejemplo, las herramientas de carburo son mejores para materiales duros.
- Inspeccionar si hay desgaste de herramientas: Revise periódicamente la herramienta para detectar signos de desgaste y reemplácela antes de que se desgaste excesivamente y sea propensa a romperse.
Abordar estos problemas comunes de configuración de herramientas requiere una combinación de capacitación adecuada, mantenimiento regular y un enfoque sistemático para la resolución de problemas. La capacidad de diagnosticar y resolver problemas relacionados con las herramientas es fundamental para lograr resultados de mecanizado eficientes y de alta calidad.
En conclusión
El proceso de configuración y optimización de herramientas de corte de torno para torneado CNC es un aspecto crucial del mecanizado que afecta significativamente la calidad, eficiencia y precisión de los procesos de fabricación. Una comprensión profunda de los componentes y funciones de las herramientas de corte, así como de los factores involucrados en la selección de herramientas, es esencial para los maquinistas y operadores de CNC.
La configuración adecuada de una herramienta de corte implica un enfoque sistemático, desde la preparación del torno y la pieza de trabajo hasta la selección del portaherramientas correcto, el montaje de la herramienta, el ajuste de la altura de la herramienta y la alineación de la línea central, y la configuración de la compensación del radio de la punta de la herramienta y las compensaciones de la herramienta. Cada paso juega un papel fundamental para lograr resultados de mecanizado precisos y eficientes.
La optimización de los parámetros de corte, incluidas las velocidades y avances, la profundidad de corte, los fluidos de corte y la gestión de la vida útil de la herramienta, es otro aspecto crítico del torneado CNC. Al seleccionar cuidadosamente los parámetros correctos, los maquinistas pueden mejorar la productividad, mantener la longevidad de la herramienta y mejorar la calidad del acabado superficial.
Finalmente, ser capaz de solucionar problemas comunes de configuración de herramientas, como vibración de herramientas, acabado superficial deficiente, imprecisiones dimensionales, problemas de control de viruta y rotura de herramientas, es esencial para mantener resultados de mecanizado consistentes y de alta calidad. Identificar estos problemas e implementar soluciones adecuadas garantiza que el proceso de mecanizado siga siendo fluido y eficiente.
En general, una comprensión integral de las herramientas de corte de torno y su configuración, combinada con la capacidad de optimizar los parámetros de corte y solucionar problemas, permite a los maquinistas lograr los mejores resultados en las operaciones de torneado CNC. El aprendizaje, la formación y la experiencia continuos son clave para perfeccionar estas habilidades y garantizar procesos de mecanizado exitosos.
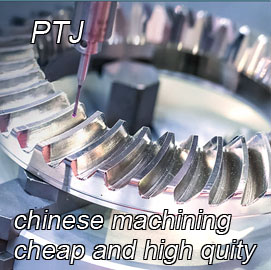
- Mecanizado de 5 ejes
- Fresado CNC
- Torneado CNC
- Industrias de mecanizado
- Proceso de mecanizado
- Tratamiento de superficies
- Mecanizado de metales
- Mecanizado de plástico
- Molde de pulvimetalurgia
- Die Casting
- Galería de piezas
- Auto partes de metal
- Partes de maquinaria
- Disipador de calor LED
- Piezas de construcción
- Partes móviles
- Partes médicas
- Componentes electrónicos
- Mecanizado a medida
- Partes de la bicicleta
- Mecanizado de aluminio
- Mecanizado de titanio
- Mecanizado de acero inoxidable
- Mecanizado de cobre
- Mecanizado de latón
- Mecanizado de súper aleación
- Mecanizado de Peek
- Mecanizado UHMW
- Unilate Mecanizado
- Mecanizado PA6
- Mecanizado PPS
- Mecanizado de teflón
- Mecanizado de Inconel
- Mecanizado de acero para herramientas
- Más material