El desarrollo y la tendencia de la tecnología de fusión por inducción al vacío.
Con el rápido desarrollo de la tecnología industrial moderna, los requisitos de las personas para el uso de piezas mecánicas son cada vez más altos, y el entorno de uso más severo presenta requisitos más altos para la resistencia a altas temperaturas, resistencia al desgaste, resistencia a la fatiga y otras propiedades de los materiales metálicos. .
Para algunos metales o materiales de aleación específicos, ya sea una prueba de I + D en etapa inicial o una producción en masa de etapa posterior y su puesta en uso, la investigación u obtención de materiales de aleación de metal de alto rendimiento requieren el apoyo de equipos de fundición de metales, equipos de tratamiento térmico de superficies, etc. Los muchos métodos especiales de calentamiento o fundición, la tecnología de calentamiento por inducción se utiliza para fundir y preparar materiales metálicos o para sinterizar y tratar térmicamente materiales en un determinado proceso, que ha desempeñado un papel vital.
Este artículo presenta el proceso de desarrollo de la tecnología de fundición por inducción al vacío y la aplicación de la tecnología de fundición por inducción en diferentes ocasiones. De acuerdo con la estructura de los diferentes tipos de hornos de inducción al vacío, compare sus ventajas y desventajas. Mirando hacia la dirección de desarrollo futuro de los hornos de inducción al vacío, expone su tendencia de desarrollo. El desarrollo y el progreso de los hornos de inducción al vacío se reflejan principalmente en la mejora gradual de la estructura general del equipo, la tendencia cada vez más obvia de modularización y el sistema de control más inteligente.
1. Tecnología de fusión por inducción al vacío
1.1 Principio
__kindeditor_temp_url__La tecnología de calentamiento por inducción generalmente se refiere a una tecnología que utiliza el principio de inducción electromagnética para obtener corriente de inducción para materiales con mejor sensibilidad magnética para lograr el propósito de calentamiento en condiciones de vacío. La corriente eléctrica pasa a través de la bobina electromagnética que rodea el material metálico a una cierta frecuencia. La corriente eléctrica cambiante genera un campo magnético inducido, que provoca una corriente inducida en el metal y genera una gran cantidad de calor para calentar el material. Cuando el calor es relativamente bajo, se puede utilizar en el tratamiento térmico por inducción al vacío y otros procesos. Cuando el calor es alto, el calor generado es suficiente para derretir el metal y usarse para preparar metales o materiales de aleación.
1.2, aplicación
1.2.1, fusión por inducción al vacío
La tecnología de fusión por inducción al vacío es actualmente la tecnología de calentamiento por inducción más eficiente, rápida, de bajo consumo, que ahorra energía y es respetuosa con el medio ambiente para calentar materiales metálicos. Esta tecnología se implementa principalmente en hornos de fusión por inducción y otros equipos y tiene una amplia gama de aplicaciones. Las materias primas de metal sólido se colocan en un crisol envuelto por una bobina. Cuando la corriente fluye a través de la bobina de inducción, se genera una fuerza electromotriz inducida y se genera una corriente parásita dentro de la carga de metal. Cuando el calor actual es mayor que la tasa de disipación de calor de la carga de metal, el calor se acumula cada vez más. Al alcanzar cierto nivel, el metal se derrite de un estado sólido a un estado líquido para lograr el propósito de fundir metales. En este proceso, dado que todo el proceso tiene lugar en un entorno de vacío, es beneficioso eliminar las impurezas de gas dentro del metal, y el material de aleación de metal obtenido es más puro. Al mismo tiempo, durante el proceso de fundición, mediante el control del entorno de vacío y el calentamiento por inducción, la temperatura de fundición se puede ajustar y la aleación de metal se puede complementar a tiempo para lograr el propósito de refinación. Durante el proceso de fusión, debido a las características de la tecnología de fusión por inducción, el material metálico líquido dentro del crisol se puede agitar automáticamente debido a la interacción de la fuerza electromagnética para hacer que la composición sea más uniforme. Esta también es una gran ventaja de la tecnología de fusión por inducción.
En comparación con la fundición tradicional, la fundición por inducción al vacío tiene grandes ventajas debido al ahorro de energía, la protección ambiental, el buen ambiente de trabajo para los trabajadores y la baja intensidad de mano de obra. Usando la tecnología de fusión por inducción, el material de la aleación final tiene menos impurezas y la proporción de la aleación agregada es más adecuada, lo que puede cumplir mejor con los requisitos del proceso para las propiedades del material.
La tecnología de fundición por inducción al vacío se ha utilizado a gran escala, desde hornos de inducción de varios kilogramos para investigación experimental hasta hornos de inducción a gran escala con una capacidad de decenas de toneladas para la producción real. Debido a su tecnología de operación simple, el proceso de fusión es fácil de controlar y la temperatura de fusión es rápida. El metal fundido tiene las ventajas de una composición uniforme, tiene grandes perspectivas de aplicación y se ha desarrollado rápidamente en los últimos años.
1.2.2, sinterización por inducción al vacío
La sinterización al vacío se refiere a la sinterización de metal, aleación o polvo compuesto de metal en productos metálicos y piezas en bruto metálicas a una temperatura por debajo del punto de fusión en un ambiente con un grado de vacío de (10-10-3Pa). Sinterizado en condiciones de vacío, no hay reacción entre el metal y el gas, y no hay influencia del gas adsorbido. El efecto de densificación no solo es bueno, sino que también puede desempeñar un papel de purificación y reducción, reduciendo la temperatura de sinterización, y la relación de sinterización a temperatura ambiente se puede reducir en 100 ℃ ~ 150 ℃. Ahorre consumo de energía, mejore la vida útil del horno de sinterización y obtener productos de alta calidad.
Para algunos materiales, es necesario realizar la unión entre partículas a través de la transferencia de átomos a través del calentamiento, y la tecnología de sinterización por inducción juega un papel de calentamiento en este proceso. La ventaja de la sinterización por inducción al vacío es que ayuda a reducir las sustancias nocivas (vapor de agua, oxígeno, nitrógeno y otras impurezas) en la atmósfera en condiciones de vacío, y evita una serie de reacciones como descarburación, nitruración, carburación, reducción y oxidación. . Durante el proceso, se reduce la cantidad de gas en los poros y se reduce la reacción química de las moléculas de gas. Al mismo tiempo, la película de óxido en la superficie del material se quita antes de que el material aparezca en la fase líquida, de modo que el material se adhiere más densamente cuando el material se funde y se adhiere, y se mejora su resistencia al desgaste. fuerza. Además, la sinterización por inducción al vacío también tiene un cierto efecto en la reducción de los costes del producto.
Debido a que el contenido de gas es relativamente bajo en un entorno de vacío, se pueden ignorar la convección y conducción de calor. El calor se transfiere principalmente desde el componente calefactor a la superficie del material en forma de radiación. La selección se basa en la temperatura de sinterización específica y las propiedades físicas y químicas del material. Los componentes de calentamiento apropiados también son muy importantes. En comparación con el calentamiento por resistencia al vacío, la sinterización por inducción adopta el calentamiento por potencia de frecuencia intermedia, lo que evita el problema de aislamiento a alta temperatura de los hornos de vacío que utilizan el calentamiento por resistencia hasta cierto punto.
En la actualidad, la tecnología de sinterización por inducción se utiliza principalmente en los campos del acero y la metalurgia. Además, en materiales cerámicos especiales, la sinterización por inducción mejora la unión de partículas sólidas, ayuda a que crezcan los granos de cristal, comprime los huecos y luego aumenta la densidad para formar cuerpos sinterizados policristalinos densos. La tecnología de sinterización por inducción también se está utilizando más ampliamente en la investigación de nuevos materiales.
1.2.3, tratamiento térmico por inducción al vacío
En la actualidad, debería haber más tecnología de tratamiento térmico por inducción concentrada principalmente en la tecnología de endurecimiento por inducción. Coloque la pieza de trabajo en el inductor (bobina), cuando una corriente alterna de cierta frecuencia pasa a través del inductor, se generará un campo magnético alterno a su alrededor. La inducción electromagnética del campo magnético alterno produce una corriente parásita cerrada en la pieza de trabajo. Debido al efecto piel, es decir, la distribución de la corriente inducida en la sección transversal de la pieza de trabajo es muy desigual, la densidad de corriente en la superficie de la pieza de trabajo es muy alta y disminuye gradualmente hacia adentro.
La energía eléctrica de la corriente de alta densidad en la superficie de la pieza de trabajo se convierte en energía térmica, lo que aumenta la temperatura de la superficie, es decir, se da cuenta del calentamiento de la superficie. Cuanto mayor sea la frecuencia de la corriente, mayor será la diferencia de densidad de la corriente entre la superficie y el interior de la pieza de trabajo, y más fina será la capa de calentamiento. Después de que la temperatura de la capa de calentamiento excede la temperatura del punto crítico del acero, se enfría rápidamente para lograr el temple de la superficie. Se puede saber por el principio del calentamiento por inducción que la profundidad de penetración de la corriente se puede cambiar de manera apropiada ajustando la frecuencia de la corriente a través de la bobina de inducción. La profundidad ajustable también es una gran ventaja del tratamiento térmico por inducción. Sin embargo, la tecnología de endurecimiento por inducción no es adecuada para piezas mecánicas complicadas debido a su escasa adaptabilidad. Aunque la capa superficial de la pieza templada tiene un esfuerzo interno de compresión mayor, la resistencia a la fractura por fatiga es mayor. Pero solo es adecuado para la producción en línea de montaje de piezas de trabajo simples.
En la actualidad, la aplicación de la tecnología de endurecimiento por inducción se utiliza principalmente en el temple superficial de manivela.ejes y camejes en la industria automotriz. Aunque estas piezas tienen una estructura simple, pero el entorno de trabajo es severo, tienen un cierto grado de resistencia al desgaste, resistencia a la flexión y resistencia al rendimiento de las piezas. Los requisitos de fatiga, a través del endurecimiento por inducción para mejorar su resistencia al desgaste y la resistencia a la fatiga, también es el método más razonable para cumplir con los requisitos de rendimiento. Es ampliamente utilizado en el tratamiento de superficies de algunas partes en la industria automotriz.
2. Equipo de fusión por inducción al vacío
El equipo de fundición por inducción al vacío utiliza tecnología de fundición por inducción para realizar el principio en el uso real mediante la combinación de la estructura mecánica. El equipo generalmente usa el principio de inducción electromagnética para colocar la bobina de inducción y el material en una cavidad cerrada, y extraer el gas en el contenedor a través de un sistema de bombeo de vacío, y luego usar la fuente de alimentación para pasar la corriente a través de la bobina de inducción a generar una fuerza electromotriz inducida y estar dentro del material Se forma un vórtice, y cuando la generación de calor alcanza un cierto nivel, el material comienza a fundirse. Durante el proceso de fusión, se realizan una serie de operaciones como control de potencia, medición de temperatura, medición de vacío y alimentación suplementaria a través de otros componentes de soporte en el equipo, y finalmente el metal líquido se vierte en el molde a través de la inversión del crisol para formar un lingote de metal. Eperlano. La estructura principal del equipo de fusión por inducción al vacío incluye las siguientes partes:
Además de los componentes anteriores, el horno de fusión al vacío también debe estar equipado con una fuente de alimentación, un sistema de control y un sistema de enfriamiento para proporcionar entrada de energía para que el equipo derrita el material y proporcione una cierta cantidad de enfriamiento en las partes clave. para evitar que el sistema se sobrecaliente y provoque una reducción o daño de la vida útil de la estructura. Para equipos de fundición por inducción con requisitos de proceso específicos, existen componentes auxiliares relacionados, como carro de transmisión, apertura y cierre de la puerta del horno, bandeja de fundición centrífuga, ventana de observación, etc. Para equipos con más impurezas, también debe estar equipado con un filtro de gas sistema, etc. Se puede ver que, además de los componentes necesarios, un conjunto completo de equipos de fusión por inducción también puede realizar diferentes funciones agregando otros componentes de acuerdo con los requisitos específicos del proceso, y proporcionar condiciones convenientes y métodos de implementación para la preparación de metales.
2.1. Horno de fusión por inducción al vacío
El horno de fundición por inducción al vacío es un equipo de fundición que primero funde el metal mediante calentamiento por inducción al vacío y luego vierte el metal líquido en un molde para obtener un lingote de metal. El desarrollo de los hornos de inducción al vacío comenzó alrededor de 1920 y se utilizó principalmente para fundir aleaciones de níquel-cromo. Hasta que la Segunda Guerra Mundial promovió el avance de la tecnología de vacío, el horno de fusión por inducción al vacío estaba realmente desarrollado. Durante este período, debido a la demanda de materiales de aleación, los hornos de fusión por inducción al vacío continuaron desarrollándose a gran escala, desde las primeras varias toneladas hasta docenas de toneladas de hornos de inducción ultragrandes. Para adaptarse a la producción en masa, además del cambio en la capacidad del equipo, la estructura del horno de inducción también ha evolucionado de un horno de ciclo con un ciclo como unidad a una fusión por inducción al vacío continua o semicontinua para carga, molde operaciones de preparación, fundición y vertido. El funcionamiento continuo sin detener el horno ahorra el tiempo de carga y el tiempo de espera para que se enfríe el lingote. La producción continua aumenta la eficiencia y también aumenta la producción de aleación. Satisfacer mejor las necesidades de la producción real. En comparación con países extranjeros, los primeros hornos de inducción al vacío de mi país tienen una capacidad relativamente pequeña, principalmente de menos de 2 toneladas. Los hornos de fundición a gran escala todavía dependen de las importaciones del exterior. Con el desarrollo de las últimas décadas, mi país también puede desarrollar la fundición por inducción al vacío a gran escala por sí mismo. Horno, la fundición máxima alcanza más de diez toneladas. El horno de fusión por inducción al vacío VIM se desarrolló anteriormente, con una estructura simple, uso conveniente y bajo costo de mantenimiento, y se ha utilizado ampliamente en la producción real.
La forma básica de un horno de fusión por inducción al vacío. Los materiales metálicos se agregan al crisol de fusión a través de una torreta giratoria. El otro lado está alineado con el crisol y la medición de temperatura se realiza insertando el termopar en el metal fundido. El metal fundido es impulsado por el mecanismo de giro y se vierte en el molde de formación para realizar la fundición del metal. Todo el proceso es sencillo y cómodo de operar. Cada fundición requiere uno o dos trabajadores para completarse. Durante el proceso de fundición, se puede lograr el monitoreo de temperatura en tiempo real y el ajuste de la composición del material, y el material metálico final está más en línea con los requisitos del proceso.
2.2. Horno de gas de membrana de inducción al vacío
Para ciertos materiales, no es necesario completar el vertido en una cámara de vacío en el proceso, solo se requiere preservación del calor y desgasificación en un ambiente de vacío. Sobre la base del horno VIM, se desarrolla gradualmente el horno de gas de membrana de inducción al vacío del horno de desgasificación VID.
La característica principal del horno de desgasificación por inducción al vacío es la estructura compacta y el pequeño volumen del horno. Un volumen más pequeño es más propicio para una extracción de gas rápida y un mejor vacío. En comparación con los hornos de desgasificación convencionales, el equipo tiene un volumen relativamente pequeño, baja pérdida de temperatura, mejor flexibilidad y economía, y es adecuado para la alimentación de líquidos o sólidos. El horno VID se puede utilizar para la fundición y desgasificación de aceros especiales y metales no ferrosos, y debe verterse en el molde en las condiciones de un entorno atmosférico o una atmósfera protectora. Todo el proceso de fundición puede realizar la eliminación de impurezas como la descarburación y refinado de materiales, deshidrogenación, desoxidación y desulfuración, lo que conduce a un ajuste preciso de la composición química para cumplir con los requisitos del proceso.
Bajo una cierta condición de vacío o atmósfera protectora, el material metálico se funde gradualmente mediante el calentamiento del horno de desgasificación por inducción, y el gas interno se puede eliminar en este proceso. Si se agrega un gas de reacción apropiado en el proceso, se combinará con el elemento de carbono dentro del metal para generar carburos gaseosos que se eliminarán del horno, logrando el propósito de descarburación y refinado. En el proceso de vertido, es necesario introducir una cierta atmósfera protectora para asegurar que el material metálico que ha sido desgasificado se aísle del gas en la atmósfera, y finalmente se complete la desgasificación y refinamiento del material metálico.
2.3. Horno de colada de desgasificación por inducción al vacío
El horno de vertido de desgasificación por inducción al vacío se desarrolla sobre la base de las dos primeras tecnologías de fundición. En 1988, Leybold-Heraeus, el predecesor de la empresa alemana ALD, fabricó el primer horno VIDP. El núcleo técnico de este tipo de horno es una cámara compacta de fusión al vacío integrada con el crisol de bobina de inducción. Es solo un poco más grande que la bobina de inducción y solo contiene la bobina de inducción y el crisol. Los cables, las tuberías de refrigeración por agua y el mecanismo de rotación hidráulica están instalados fuera de la cámara de fusión. La ventaja es proteger los cables y las tuberías refrigeradas por agua de los daños causados por las salpicaduras de acero fundido y los cambios periódicos de temperatura y presión. Debido a la conveniencia de desmontar y facilitar la sustitución del crisol, la carcasa del horno VIDP está equipada con tres cuerpos de horno. Un revestimiento de horno de crisol de preparación acorta el ciclo de producción y mejora la eficiencia de producción.
La tapa del horno se apoya en el marco del horno y dos columnas de cilindros hidráulicos mediante sellado al vacío. cojinetes. Al verter, dos cilindros hidráulicos cubren la tapa del horno en el lateral, y la tapa del horno impulsa la cámara de fusión para que se incline alrededor del vacío. cojinete. En el estado de vertido inclinado, no hay movimiento relativo entre la cámara de fusión y el crisol de bobina de inducción. El corredor es una parte importante del horno VIDP. Debido a que el diseño del horno VIDP aísla la cámara de fusión de la cámara de lingotes, el acero fundido debe pasar a través del canal de vacío hacia la cámara de lingotes. La cámara de lingotes está abierta y cerrada con un lado oblicuo cuadrado. Está compuesto por dos partes. La parte fija es adyacente a la cámara de deslizamiento y la parte móvil se mueve horizontalmente a lo largo de la pista del suelo para completar la apertura y cierre de la cámara de lingotes. En algunos equipos, la parte móvil está diseñada para estar a 30 grados, abierta de izquierda a derecha hacia arriba, lo que es conveniente para cargar y descargar lingoteras y para el mantenimiento y reparación diarios de grúas. Al comienzo de la fundición, el cuerpo del horno se levanta mediante el mecanismo hidráulico de abajo, se une con la cubierta del horno de la estructura superior del horno y se bloquea con un mecanismo especial. El extremo superior de la tapa del horno está conectado con la cámara de alimentación a través de un vacío. válvula.
Dado que solo la parte de fundición está encerrada en la cámara de vacío y se vierte a través de la ranura de desviación, la estructura del horno es compacta, la cámara de fusión es más pequeña y el vacío se puede controlar mejor y más rápido. En comparación con el horno de fusión por inducción tradicional, tiene las características de un tiempo de evacuación corto y una tasa de fuga baja. El control de presión ideal se puede lograr equipando el sistema de control lógico PLC. Al mismo tiempo, el sistema de agitación electromagnética puede agitar de manera estable la piscina fundida, y los elementos añadidos se disolverán uniformemente en la piscina fundida de arriba a abajo, manteniendo la temperatura casi constante. Al verter dinero, el canal se calienta mediante el sistema de calefacción externo para reducir el bloqueo de vertido inicial del puerto de vertido y el agrietamiento térmico del canal. Al agregar un deflector de filtro y otras medidas, puede aliviar el impacto del acero fundido y mejorar la pureza del metal. Debido al pequeño volumen del horno VIDP, la detección y reparación de fugas de vacío son más fáciles y el tiempo de limpieza en el horno es más corto. Además, la temperatura en el horno se puede medir con un termopar pequeño y fácil de reemplazar.
2.4, crisol refrigerado por agua por inducción
El método de fundición por levitación al vacío por inducción electromagnética de crisol refrigerado por agua es un método de fundición que se ha desarrollado rápidamente en los últimos años. Se utiliza principalmente para preparar materiales metálicos o no metálicos de alto punto de fusión, alta pureza y extremadamente activos. Al cortar el crisol de cobre en partes iguales de la estructura de pétalos de cobre, y el enfriamiento por agua pasa a través de cada bloque de pétalos, esta estructura mejora el empuje electromagnético, de modo que el metal fundido se aprieta en el medio para formar una joroba y separarse del pared del crisol. El metal se coloca en un campo electromagnético alterno. El dispositivo concentra la capacidad en el espacio de volumen dentro del crisol y luego forma una fuerte corriente parásita en la superficie de la carga. Por un lado, libera calor Joule para derretir la carga, y por otro lado, forma la fuerza de Lorentz para derretir El cuerpo se suspende y produce una fuerte agitación. Los elementos de aleación añadidos se pueden mezclar rápida y uniformemente en la masa fundida, haciendo que la composición química sea más uniforme y la conducción de la temperatura más equilibrada. Debido al efecto de la levitación magnética, la masa fundida está fuera de contacto con la pared interior del crisol, lo que evita que el crisol contamine la masa fundida. Al mismo tiempo, reduce la conducción de calor y mejora la radiación de calor, lo que reduce la disipación de calor del metal fundido y alcanza una temperatura más alta. Para la carga de metal adicional, se puede derretir y mantener caliente según el tiempo requerido y la temperatura establecida, y no es necesario procesar la carga por adelantado. La fundición de crisol refrigerado por agua puede alcanzar el nivel de fundición por haz de electrones en términos de eliminación de inclusiones metálicas y refinación de desgasificación, mientras que la pérdida por evaporación es menor, el consumo de energía es menor y la eficiencia de producción se mejora. Debido a las características de calentamiento sin contacto del calentamiento por inducción, el impacto sobre la masa fundida es menor y tiene un buen efecto en la preparación de metales de mayor pureza o extremadamente activos. Debido a la compleja estructura del equipo, todavía es difícil realizar la fundición maglev para equipos de gran capacidad. En esta etapa, no existe un equipo de fundición de crisol de cobre refrigerado por agua de gran capacidad. El actual equipo de crisol refrigerado por agua solo se utiliza para la investigación experimental sobre la fundición de metales de pequeño volumen.
3. La tendencia de desarrollo futuro de los equipos de fusión por inducción
Con el desarrollo de la tecnología de calentamiento por inducción al vacío, los tipos de hornos cambian constantemente para lograr diferentes funciones. De una simple estructura de fundición o calefacción, se ha convertido gradualmente en una estructura compleja que puede realizar diferentes funciones y es más propicia para la producción. Para procesos tecnológicos más complejos en el futuro, cómo lograr un control preciso del proceso, medir y extraer información relevante y reducir los costos laborales tanto como sea posible es la dirección de desarrollo de los equipos de fusión por inducción.
3.1, modulares
En un conjunto completo de equipos, diferentes componentes están equipados para diferentes requisitos de uso. Cada parte del componente realiza su propia función para lograr su propio propósito de uso. Para ciertos tipos de hornos, agregar ciertos módulos para hacer el equipo más completo, por ejemplo, equipado con un sistema completo de medición de temperatura ayuda a observar los cambios de los materiales en el horno con la temperatura, y lograr un control más razonable de la temperatura; equipado con un espectrómetro de masas para detectar la composición del material Ajustar el tiempo y la secuencia de adición de elementos de aleación para mejorar el desempeño de la aleación en la etapa de desarrollo del proceso; equipado con un cañón de electrones y un cañón de iones para resolver el problema de la fusión de algunos metales refractarios, etc. En los equipos metalúrgicos de inducción del futuro, las diferentes combinaciones de diferentes módulos para lograr diferentes funciones y cumplir con diferentes requisitos de procesos se han convertido en una tendencia inevitable de desarrollo, y también es una combinación y referencia de diferentes campos. Para mejorar el proceso de fundición de metales y obtener materiales con mejor desempeño, los equipos modulares tendrán una mayor competitividad en el mercado.
3.2. Control inteligente
En comparación con la fundición tradicional, el equipo de inducción al vacío tiene una gran ventaja para realizar el control del proceso. Debido al desarrollo de la tecnología informática, el funcionamiento amigable de la interfaz hombre-máquina, la adquisición inteligente de señales y la configuración razonable del programa en el equipo pueden lograr fácilmente el propósito de controlar el proceso de fundición, reducir los costos laborales y hacer que la operación sea más simple y sencilla. conveniente.
En el desarrollo futuro, se agregarán sistemas de control más inteligentes al equipo de vacío. Para el proceso establecido, será más fácil para las personas controlar con precisión la temperatura de fundición a través del sistema de control inteligente, agregar materiales de aleación en un momento específico y completar una serie de acciones de fundición, preservación del calor y vertido. Y todo esto será controlado y registrado por la computadora, reduciendo pérdidas innecesarias causadas por errores humanos. Para el proceso de fundición repetitivo, puede realizar un control moderno más conveniente e inteligente.
3.3. Informatización
El equipo de fundición por inducción generará una gran cantidad de información de fundición durante todo el proceso de fundición, los cambios de parámetros en tiempo real de la fuente de alimentación de calentamiento por inducción, el campo de temperatura de la carga, el crisol, el campo electromagnético generado por la bobina de inducción, el propiedades físicas del metal fundido, etc. En la actualidad, el equipo solo realiza una recopilación de datos simple, y el proceso de análisis se lleva a cabo después de que se extraen los datos después de que se completa la fundición. En el futuro, el desarrollo de la informatización, la recopilación y procesamiento de datos y el proceso de análisis estarán inevitablemente casi sincronizados con el proceso de fundición. Recopilación completa de datos para los materiales fundidos internamente de equipos metalúrgicos, procesamiento informático de datos, visualización en tiempo real del campo de temperatura interna y campo electromagnético del equipo en la situación actual y transmisión de señales, a través de la retroalimentación en tiempo real de diferentes datos. conveniente para las personas La observación y el ajuste en tiempo real del proceso de fundición fortalecieron la intervención y el control humanos. En el proceso de fundición, se realizan ajustes oportunos para mejorar el proceso y mejorar el rendimiento de la aleación.
Conclusión 4
Con el progreso de la industria, la tecnología de fusión por inducción al vacío se ha desarrollado enormemente en las últimas décadas con sus ventajas únicas y juega un papel importante en el campo industrial. En la actualidad, aunque la tecnología de fundición por inducción al vacío de mi país todavía está por detrás de la de países extranjeros, todavía requiere los esfuerzos incansables de los profesionales pertinentes para mejorar la competitividad del mercado de los equipos de fundición especiales de mi país y hacer todo lo posible para convertirse en el equipo de fundición de primera clase del mundo. . Primer plano.
Enlace a este artículo: El desarrollo y la tendencia de la tecnología de fusión por inducción al vacío.
Declaración de reimpresión: si no hay instrucciones especiales, todos los artículos de este sitio son originales. Indique la fuente de la reimpresión: https: //www.cncmachiningptj.com
PTJ® es un fabricante personalizado que ofrece una gama completa de barras de cobre, piezas de latón y partes de cobre. Los procesos de fabricación comunes incluyen corte, estampado, calderería, servicios de electroerosión por cable, grabado, conformado y doblado, trastornado, caliente forja y prensado, perforado y punzonado, laminado y moleteado de hilos, cizallado, mecanizado de husillos múltiples, extrusión y forja de metal y estampado. Las aplicaciones incluyen barras colectoras, conductores eléctricos, cables coaxiales, guías de ondas, componentes de transistores, tubos de microondas, tubos de molde en blanco y Metalurgia de polvos tanques de extrusión.
Cuéntanos un poco sobre el presupuesto de tu proyecto y el tiempo de entrega esperado. Crearemos una estrategia con usted para brindarle los servicios más rentables para ayudarlo a alcanzar su objetivo. Puede contactarnos directamente ( ventas@pintejin.com ).
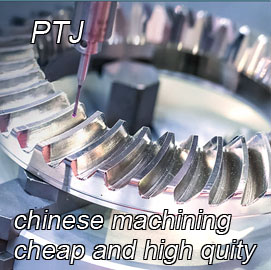
- Mecanizado de 5 ejes
- Fresado CNC
- Torneado CNC
- Industrias de mecanizado
- Proceso de mecanizado
- Tratamiento de superficies
- Mecanizado de metales
- Mecanizado de plástico
- Molde de pulvimetalurgia
- Die Casting
- Galería de piezas
- Auto partes de metal
- Partes de maquinaria
- Disipador de calor LED
- Piezas de construcción
- Partes móviles
- Partes médicas
- Componentes electrónicos
- Mecanizado a medida
- Partes de la bicicleta
- Mecanizado de aluminio
- Mecanizado de titanio
- Mecanizado de acero inoxidable
- Mecanizado de cobre
- Mecanizado de latón
- Mecanizado de súper aleación
- Mecanizado de Peek
- Mecanizado UHMW
- Unilate Mecanizado
- Mecanizado PA6
- Mecanizado PPS
- Mecanizado de teflón
- Mecanizado de Inconel
- Mecanizado de acero para herramientas
- Más material